In recent years, fancy consumer-facing technologies have dominated global headlines.
The rise of cryptocurrencies and NFTs, the advent of the metaverse, and most recently, the emergence of Generative AI and Large Language Models like ChatGPT have all captivated our collective imagination.
Yet, as exciting as (some) of these advancements are, they overshadow a less heralded but potentially more transformative shift.
Quietly unfolding in the background, the Fourth Industrial Revolution, aka Industry 4.0, holds the potential to redefine global industrial production on a scale perhaps unseen before.
This next era of the digitized manufacturing sector is characterized by disruptive trends, including the rise of data and connectivity, analytics, human-machine interaction, and improvements in robotics.
Now, you might be thinking, „Hold up, hasn’t Industry 4.0 been around for a while? Why should I sit up and pay attention now?“
You’re absolutely right.
A quick Google Trends check reveals that, as far back as 2015, Industry 4.0 has been a buzzing keyword.
Its cousins, „Smart Factory“ and „Digital Factory,“ have been trending even longer.
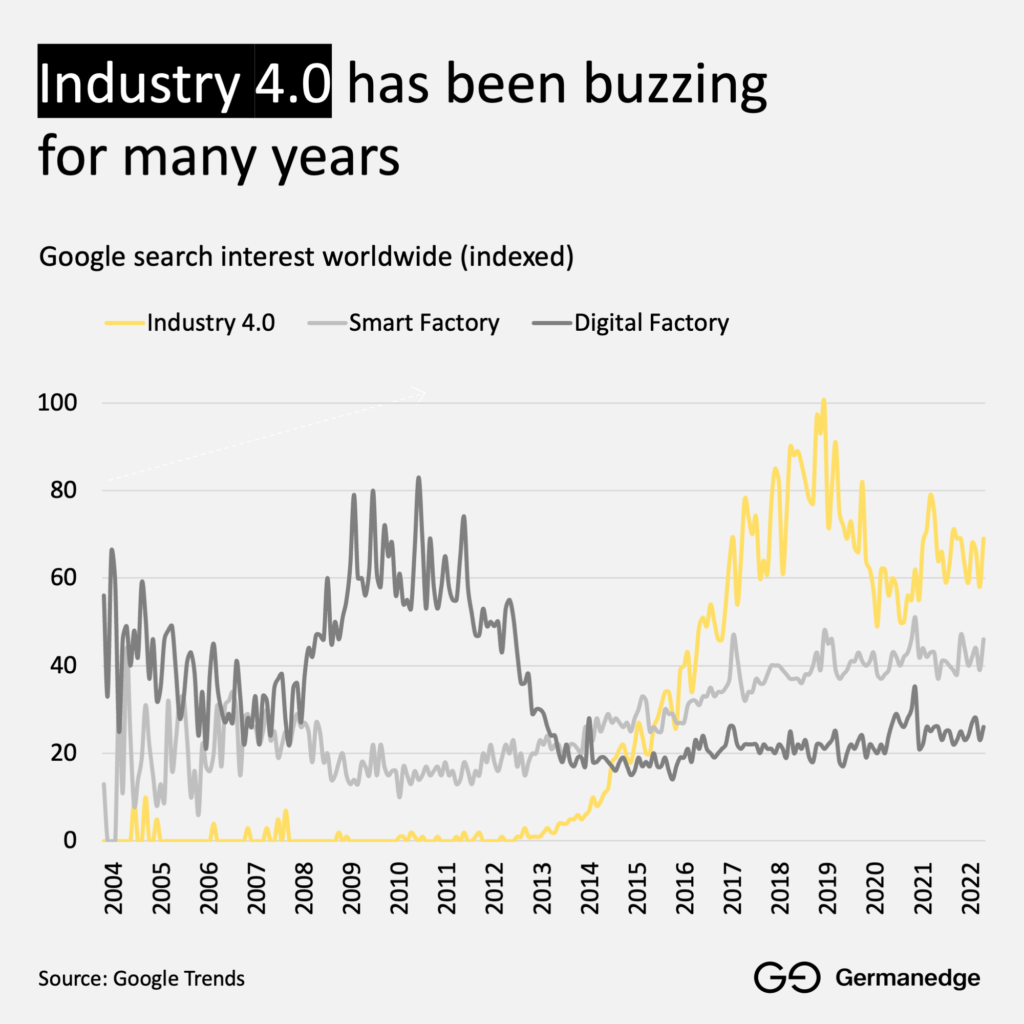
So, why am I bringing your attention towards a concept that’s almost a decade old? Here’s the catch.
While the idea of Industry 4.0 isn’t new, its relevance today, in 2023, is the most significant to date.
In fact, 2023 might be the year when we see the scales tip, pushing smart industrial production into an unprecedented technology era.
Why is this the case? Let’s take a closer look.
Before we get started, let me demonstrate to you that I’m not the only business leader that believes Industry 4.0 is more mission-critical today than ever before.
CEOs‘ New Priority: Industry 4.0
Understanding the new emphasis on Industry 4.0 is as easy as tuning into the conversations taking place in corporate boardrooms.
What CEOs discuss is arguably more indicative of the future than Google Trends, reflecting the strategic priorities of industry leaders rather than fleeting consumer interests.
How do we tap into these conversations?
Thankfully, IoT Analytics has done the heavy lifting for us.
In a comprehensive analysis of Q1/2023 earnings calls from over 3,000 US-listed companies, Industry 4.0 emerged as one of the hottest topics among corporate leaders.
In fact, as the chart below illustrates, Industry 4.0 was the second fastest-growing topic, edged out only by AI and ChatGPT.
- In a striking uptick, “industrial automation” was discussed 57% more than in the previous quarter.
- Even more impressive, the term “predictive maintenance” witnessed a whopping increase of 136%.
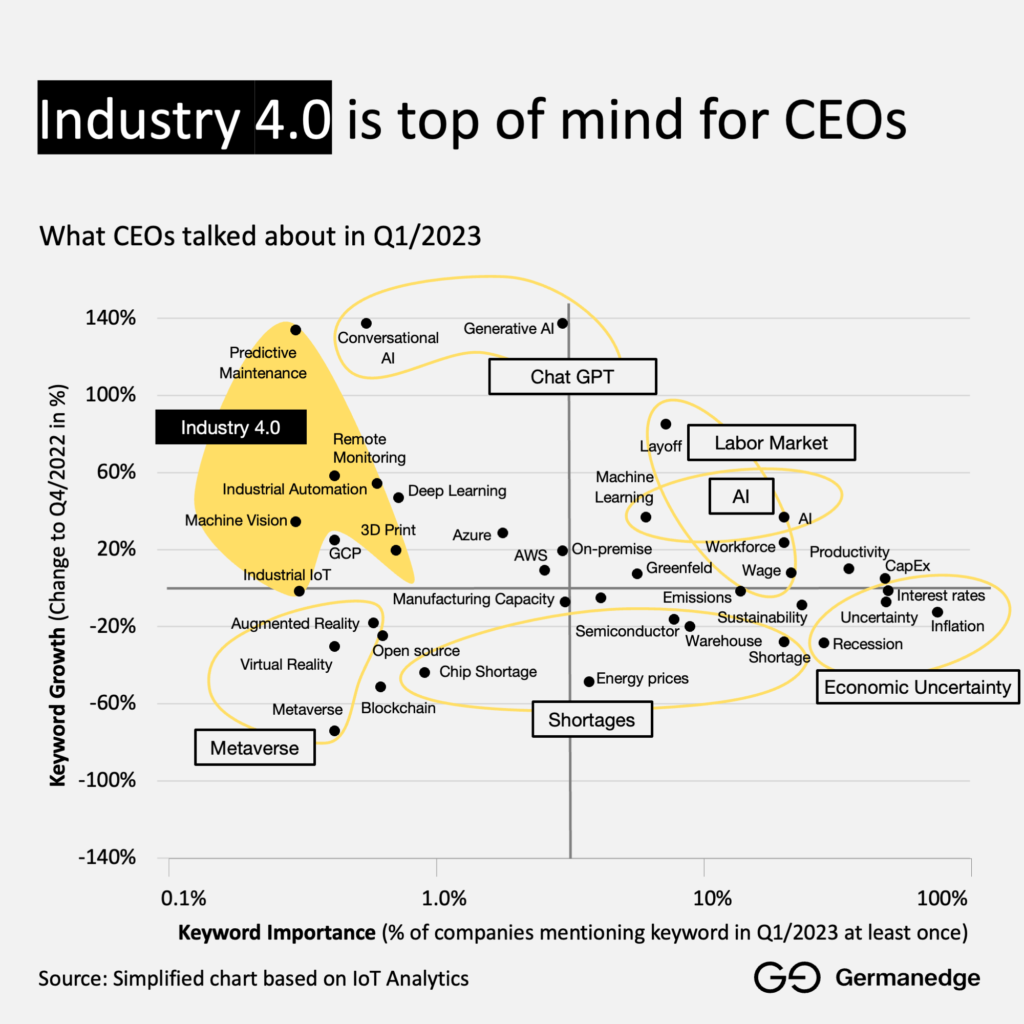
Why is this significant?
Simply put, the themes that captivate boardrooms are strong indicators of future investment directions. The rising chorus around Industry 4.0 suggests a pressing need to accelerate investments and shift from proof-of-concept to ROI-driven, outcome-based deployments.
Emerging technologies like connectivity tech, big data analytics, centralized and remote-controlled monitoring, and process automation are poised to attract substantial investments in the near future.
So, while consumer-facing tech trends may command the spotlight, the industrial trend making waves in the corporate world is unequivocally Industry 4.0.
Now that we’ve established the prominence of Industry 4.0 in corporate dialogue, let’s delve deeper into the drivers propelling its relevance.
There are three key factors that help us unravel this scenario.
1. Pandemic Response: Industry 4.0 Shows Its Strength
The first intriguing force that has propelled the acceleration of Industry 4.0 is its demonstrated value during the COVID-19 pandemic. In 2020, as the world grappled with an unprecedented health and economic crisis, industrial digitization was put to the ultimate test.
Manufacturing companies across various industries faced extraordinary challenges, from worker and raw material shortages to sudden demand surges.
Did Industry 4.0 technologies rise to the occasion?
The answer, according to a recent McKinsey survey, is a resounding “yes.”
Companies that had already implemented Industry 4.0 use cases prior to the pandemic found themselves better equipped to navigate the crisis, as illustrated in the chart below.
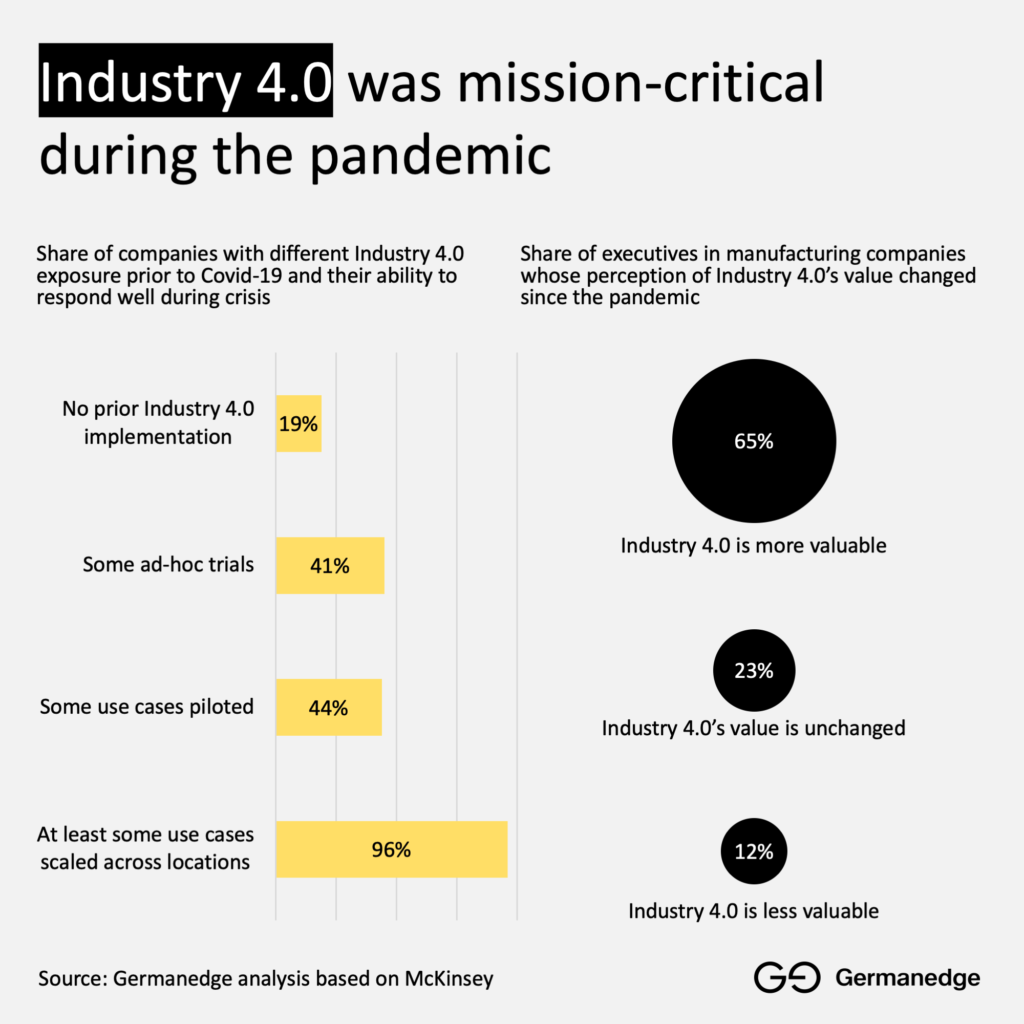
A prime example of this would be a company that had a digital twin of its supply chain.
During the pandemic, this digital twin allowed the company to simulate multiple scenarios, effectively preparing itself for potential shutdowns of manufacturing locations or disruptions in raw material supply. These preparations were invaluable in maintaining operational resilience amid such an unpredictable period.
Such success stories have sparked an intensified interest in the potential of Industry 4.0 technologies, further driving the momentum towards this transformative shift in industrial production.
2. Robotics: Reaching Never-Before-Seen Productivity
The second reason pointing to 2023 as the tipping point for Industry 4.0 lies in the unprecedented levels of technology adoption within leading factories and warehouses, leading to remarkable productivity enhancements.
To illustrate this, let’s take a closer look at Amazon, the e-commerce titan known for its relentless pursuit of efficiency in its warehouses and distribution centers.
A report by ARK Invest reveals a striking advancement in Amazon’s use of robotics.
- Seven years ago, the champion robot in the Amazon picking challenge could pick 30 items in an hour.
- Fast forward to 2022, and Amazon boasts a robot prototype capable of picking 1,000 items per hour – a staggering 33x productivity improvement that now outpaces human capabilities.
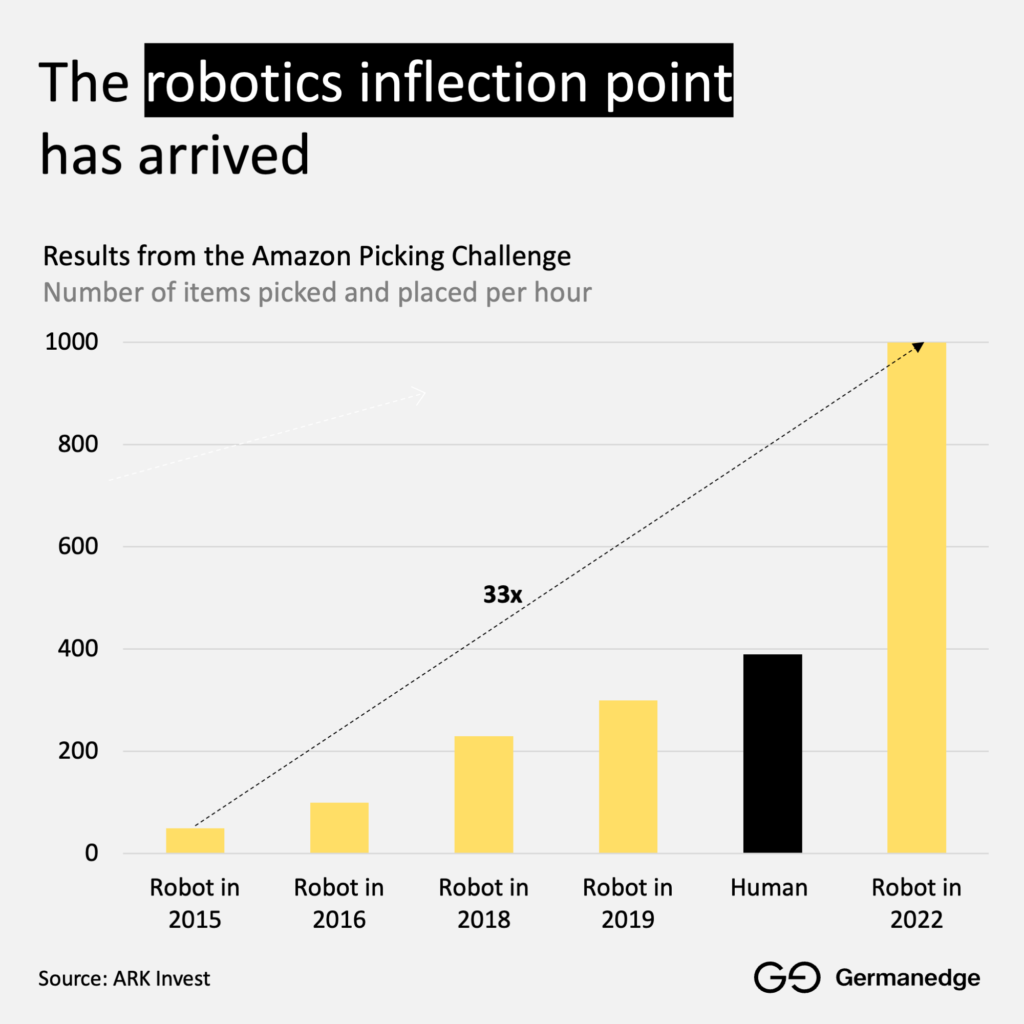
The ramifications of this advancement are profound.
This productivity revolution isn’t about replacing humans but rather enhancing their capabilities. Amazon, for instance, is not only increasing its robotic fleet but also hiring more human workers. In 2022, Amazon’s robotic fleet grew by 49% while the number of human employees increased by 24%.
This trend towards a blend of humans and robots, often referred to as “cobots,” is vital to the future of Industry 4.0. Cobots don’t just help with tasks that are dangerous or monotonous for human workers. They also enhance productivity, enabling humans to focus on tasks that require creativity, problem-solving, and human interaction.
The productivity boost provided by this harmonious blend of human and machine is one of the key reasons why Industry 4.0 is at an inflection point in 2023.
The rise of robotics and connected workers is ushering in a new era of productivity and efficiency that was once thought impossible.
3. Quality Assurance & Sustainability: Elevating Standards in Global Competition
Let’s look at the final element that is accelerating Industry 4.0.
In today’s globalized and competitive markets, two factors have risen to prominence as crucial differentiators: quality and sustainability.
- In the race to win customers, subpar quality can no longer be hidden behind clever marketing or competitive pricing.
- Additionally, customers are not only demanding superior quality but are also becoming increasingly aware of environmental issues, thus seeking products that are created through sustainable and efficient production methods.
Industry 4.0 is playing a pivotal role in addressing both these factors.
Smart factory automation, a key component of Industry 4.0, has already revolutionized quality assurance, see chart below, but it is yet to show its impact on the way we approach sustainability.
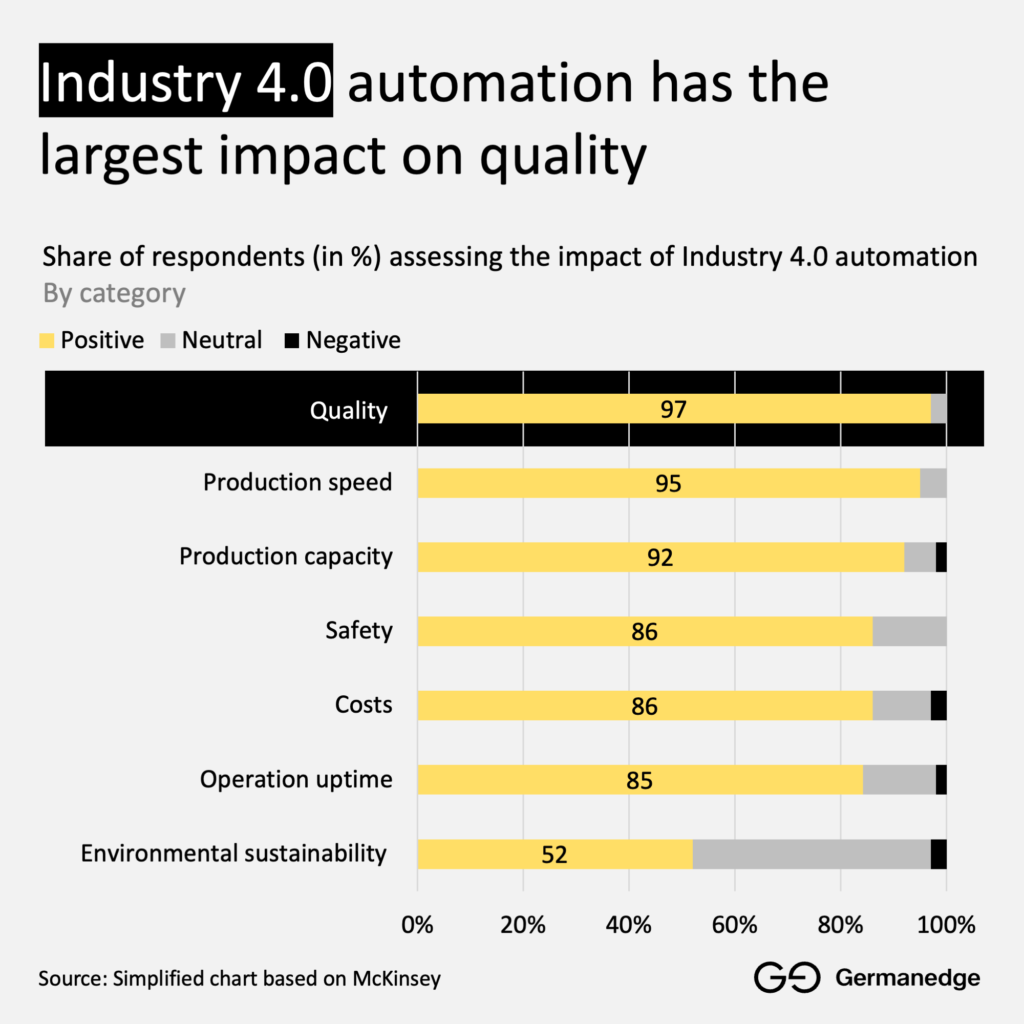
As the chart shows, a recent survey of 65 senior leaders and executives from manufacturing companies confirmed the massive impact of automation on quality, with a staggering 97% endorsing its positive effect. This impact outpaced other critical factors such as production speed (95%), production capacity (92%), safety (86%), and costs (86%).
However, the advancement towards more environmentally friendly production through automation is still limited, with only half of the respondents acknowledging its beneficial influence on sustainable practices.
My core thesis is that “Sustainable production represents Industry 4.0’s next major frontier.”
And actually, the data is on my side.
A striking new report reveals that none of the world’s top industrial sectors would be profitable if they fully integrated environmental costs. This underlines the urgent need for incorporating externalities into our economic modeling and transitioning towards more sustainable production methods.
Industry 4.0 technologies like real-time monitoring, predictive maintenance, and advanced analytics are the keys to this transition. They contribute to more efficient, less wasteful production, aligning industrial processes with the environmental imperatives of our time.
As we venture further into 2023, maintaining high-quality standards while embracing sustainability is not just an aspiration; it’s a necessity.
With Industry 4.0 at the helm, companies are poised to achieve this dual goal, carving their
path in the global competitive landscape.
Act Now: Embrace the Future
Industry 4.0 is here.
And it’s reshaping our global industrial production landscape. As we teeter on the brink of this transformative era, the pressing question isn’t “if” but “how swiftly” we can harness this inevitable change.
Past trends have shown that early adopters of these technologies are better equipped to steer through challenges and seize opportunities. But to successfully navigate this transformation, a reliable partner is essential — a partner like Germanedge.
Living up to our mantra of “creating the perfect flow,” we offer innovative software solutions that empower companies to produce more intelligently, more flexibly, and more sustainably.
We provide not just the tools but also the vision to ensure maximum efficiency at all times and at every point in your production process.
With Germanedge, you’re not simply upgrading your capabilities, but future-proofing your operations. We guide you in defining the optimal blueprint for a digital factory, eliminating unnecessary detours and blind alleys on your path to Industry 4.0.
The time to act is now.
Embrace the future of connected production. Unlock the potential of Industry 4.0.