In this blog post, we would like to introduce you to the IT/OT trends for 2025 so that you can take away new knowledge about how these trends will revolutionize your production processes. We will show you the key technology trends that will have a lasting impact on the shopfloor.
Find out how you can use digital solutions not only to overcome challenges such as the shortage of skilled workers and flexible production requirements, but also to increase your efficiency and agility.
Trend 1: Digital solutions for the skills shortage
The manufacturing industry is facing an unprecedented labor shortage, characterized by a significant lack of skilled workers and employee retention issues.
Recent data shows that 76% of manufacturers report significant staffing problems, with average employee tenure dropping from 20 years to 3 years and job tenure falling from 7 years to just 9 months. The crisis has worsened to such an extent that 31% of companies are turning to outsourcing as a solution.
However, companies can also counteract the shortage of skilled workers through targeted IT implementations. These include, for example, the launch of digital training and knowledge management systems, the use of augmented reality (AR) solutions for remote support and the development of intuitive, user-friendly interfaces for complex machines.
The integration of systems for the automation of work processes, the implementation of digital work instructions and standard operating procedures (SOPs), as well as the creation of digital twin environments for training and simulation also help.
This results in the following benefits:
- Accelerated onboarding and training processes
- Reduced dependence on expert knowledge
- Improved knowledge retention and transfer
- Increased employee productivity and efficiency
- Reduced training costs
- Increased operational resilience
- Better documentation and standardization of processes
- Improved occupational safety through digital support
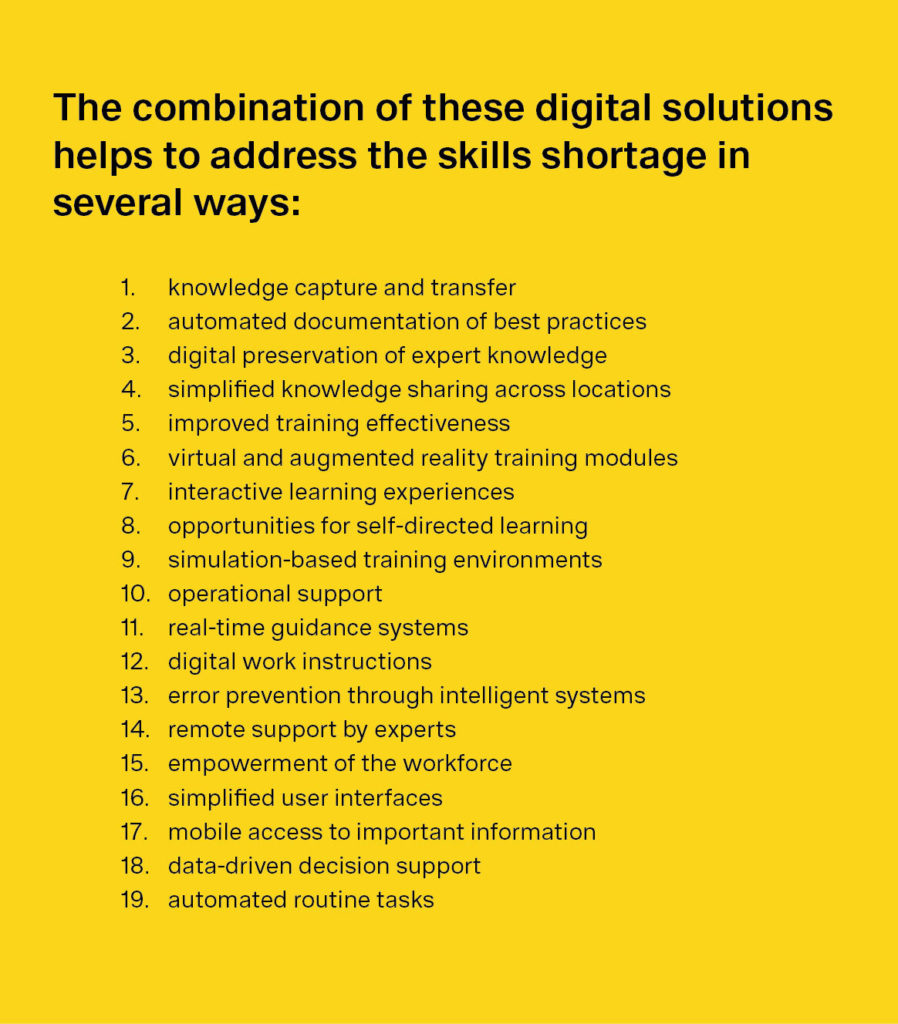
For companies looking to address the skills shortage while maintaining productivity and quality standards, the launch of these digital solutions is an important strategic initiative. Investing in digital technologies not only helps to bridge the current skills shortage, but also positions manufacturers for future HR challenges and opportunities.
For more insights into digital twin technology and its impact, read IoT Analytics’ comprehensive market analysis.
Trend 2: Decentralized production models
The global manufacturing landscape has changed significantly in recent years. The trend of bringing production closer to home, diversifying supply chains and adapting to policy changes is reshaping the industry. Here are some of the key developments driving this change:
1. home production – bringing manufacturing back home
The push to bring manufacturing back home has reached new heights, particularly in the US. An impressive 364,000 new manufacturing jobs were created there in 2022 alone. This trend is expected to gain further momentum, especially with policy changes that could encourage additional investment in domestic industry. The aim is to strengthen national economies, create jobs and reduce dependence on foreign production.
2. diversification of suppliers for more resilience
The vulnerability of global supply chains has become increasingly apparent in recent years, prompting companies to adopt a “China-plus-one” strategy. By diversifying their supply chain base, companies are trying to minimize risks that can arise from dependence on a single country. This strategy not only strengthens the resilience of supply chains, but also ensures continuity in the event of geopolitical or economic disruptions.
3. dealing with global rules and regulations
Global regulations and changing tariffs are changing the economics of manufacturing. Companies are responding by re-evaluating their production strategies to adapt to the new trade guidelines. The focus is on remaining competitive while meeting regulatory compliance requirements.
4. customer proximity as a competitive advantage
For smaller manufacturers, proximity to customers becomes a key advantage. Manufacturing close to customers allows companies to respond quickly to demands, customize products to local preferences and ensure strict quality control. This proximity fosters stronger customer relationships and increases satisfaction.
5. The rise of micro-factories and smaller production units
To adapt to changing market demands, micro-factories and smaller production units are becoming increasingly important. These agile manufacturing approaches allow companies to scale efficiently, reduce waste and respond quickly to market trends. This flexibility and adaptability allows manufacturers to remain competitive in a dynamic environment.
To integrate decentralized production models into your operations, you need cloud-based manufacturing execution systems (MES) that can manage multiple sites. Likewise, cybersecurity measures for distributed networks need to be improved. Remote monitoring and management capabilities should be integrated, and IT infrastructure should be standardized across multiple sites.
This will result in the following benefits:
- Reduced logistics costs and transportation times
- Increased resilience of the supply chain
- Better response to local market requirements
- Reduced risk from geopolitical disruptions
- Improved sustainability through reduced transportation emissions
- Greater flexibility in production scaling
The shift towards domestic production, diversified supply chains and customer-centric manufacturing marks the beginning of a new era of industrial innovation. Companies that embrace these trends not only ensure their future viability, but also contribute to a more resilient and sustainable global economy. The return to local production and the launch of agile manufacturing models are creating exciting opportunities for companies and economies around the world.
Trend 3: Unifies Named Space: the data revolution
A Unified Named Space creates a standardized system for identifying and accessing all data points in production across the entire company. It provides a common language for the communication of devices, sensors and systems, breaks down data silos and enables the seamless integration of the estimated 21 billion IoT devices.
Standardized naming conventions are being launched and data integration platforms developed for this purpose. Central data lakes or data grid architectures are being created and the framework for data management is being improved. In addition, investments must be made in a high level of network infrastructure.
This results in the following advantages:
- Simplified system integration
- Improved data availability and analysis
- Improved cross-functional collaboration
- Better decision-making through comprehensive data transparency
- Easier implementation of digital twins (predicted CAGR of 30% 2023-2027)
- Lower costs for maintenance and integration
Trend 4: Agile IT implementation
Agile IT implementation in manufacturing means moving away from traditional waterfall project management towards an iterative, flexible approach. It involves breaking down large IT projects into smaller, manageable pieces that can be implemented and tested quickly, with continuous feedback and adaptation.
This involves launching DevOps processes for production systems, implementing continuous integration/continuous delivery (CI/CD) pipelines and forming cross-functional teams. Modular system architectures must also be developed and investments made in test automation.
This results in the following advantages:
- Faster time-to-value for IT projects
- Lower risk due to gradual implementation
- Better alignment with business requirements
- Greater involvement of stakeholders
- More flexible response to changing requirements
- Improved project success rates
Trend 5: The rise of agentic AI
Agentic AI represents a paradigm shift in manufacturing intelligence. These autonomous systems go beyond traditional AI by: performing independent quality analysis, creating automated compliance reports, making real-time decisions and optimizing continuous processes.
Key applications include:
- Quality Analysis Agents: Real-time defect detection and compliance monitoring
- Reporting Agents: Automated generation of comprehensive quality audit reports
- Process optimization: Continuous improvement through data-driven insights
The convergence of all these trends is leading to a more resilient, efficient and adaptable manufacturing ecosystem. Companies that successfully implement these changes will be better positioned to:
- Overcome workforce challenges
- Respond quickly to market changes
- Optimize operations through data-driven decisions
- Maintain competitive advantage in a rapidly evolving industry
Successfully managing this change will require a strategic approach to technology launch, sound change management and continued investment in systems and people. As we move towards 2025, manufacturers must carefully balance these elements while maintaining operational performance and meeting customer demands.
The role of IT leaders in manufacturing organizations will become increasingly important as they navigate these complex changes while ensuring security, reliability and performance in increasingly distributed and data-intensive operations.
Would you like to find out more about these trends and how you can revolutionize your digital production? Then register for our webinar “IT/OT Trends 2025 for the shopfloor”!